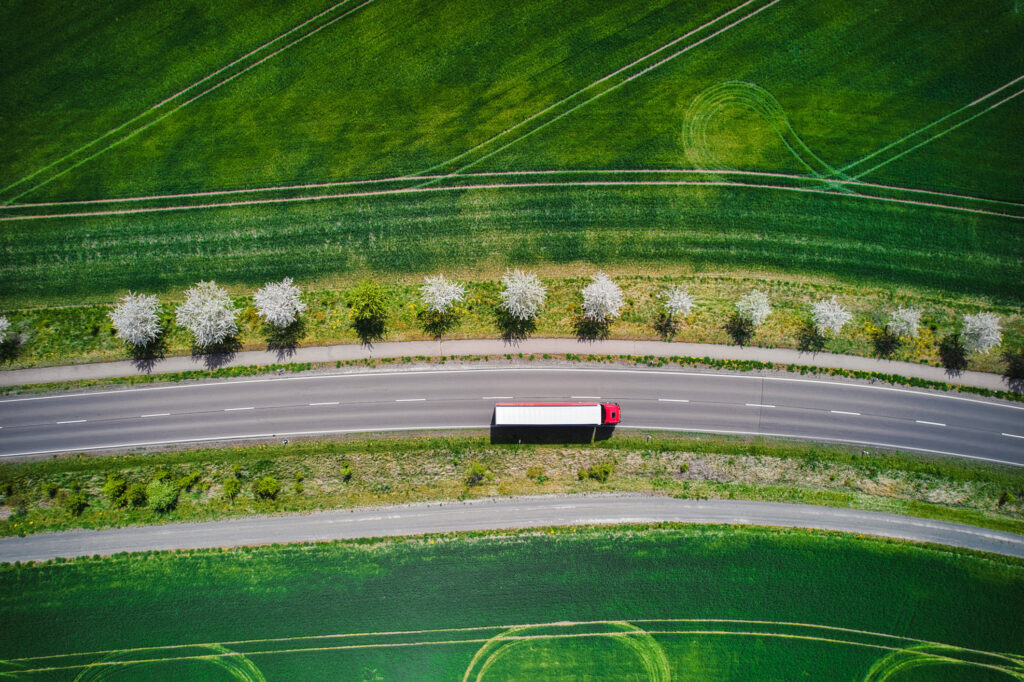
Developing infrastructure remains a key focus for global departments of transportation, with conservative estimates placing new road construction projects at a value of $3.4 trillion. The global market for asphalt production is expected to reach 138 million tons by 2027. Simultaneously, 107 countries have also made pledges to pursue net-zero emissions according to the United Nations. Â
Â
At the crossroads of the conversation between construction and conservation are the emissions produced by asphalt roadway development. Eighty-five percent of all bitumen, a byproduct of the oil refining process and a non-renewable resource, is used in asphalt paving, and bitumen production remains a key contributor to carbon emissions. With all of these factors at play, many advocates are asking whether sustainable asphalt is a realistic aim.Â
Â
Asphalt as Recycled Material for Sustainable PavingÂ
Uniquely, asphalt roadway surfaces can be 100% recycled. As older roadway surfaces fail, they are excavated or milled with heavy machinery to remove the surface layer. This material can then be delivered to a plant site where it can be processed into what is known as reclaimed asphalt pavement (RAP). Â
Â
To do this, the roadway material is screened to remove foreign objects from the lot. The remaining aggregates are crushed into smaller pieces and then fractionated based on particle sizes. When a plant is ready to use RAP in a mix, the aggregate is homogenized to create a uniform composition. The resulting material is then used in a new asphalt mix. Â
Â
In the United States, 95% of RAP is put to use in new mixes, accounting for over 94.6 million tons. Similar trends are evolving in Europe, where 76% of 36 million tons of RAP was re-used in new paving projects in 2022. Â
Â
All of this RAP use can help lead to overall lower carbon emissions attributed to new roadway construction projects. With RAP use comes a reduced need for not only virgin aggregates but also virgin bitumen or binder in mix. Â
Â
Limitations of Using RAP in New Roadway DevelopmentÂ
While RAP usage promises to help further sustainability goals, the material has its limitations. RAP particles contain both aggregate, which does not notably change over time, and bitumen, which through aging experiences deterioration of its physical and chemical binder properties. This means that only so much RAP can be included in a mix before additional virgin binder is needed to bring it all together. The traditional threshold for this has been 25% RAP, and the limitations of RAP usage by various departments of transportation reflect this. The average amount of RAP used within the United States is 21.9%. In Europe, these limits have been typically lower: France at 12.8%, Austria at 10.5%, and Hungary at 3.2%.Â
Â
A viable binder, unlike the aged binder found in RAP, is critical for extended roadway performance. Binders keep aggregate particles together to provide stability and durability such as resistance to cracking, rutting, and fatigue. Using poor quality binder or aged binder in a mix can compromise the integrity of the roadway. In laboratory testing, many of these high-RAP mixes would fail to meet DOT specifications and would never be used in a real-world roadway application. Â
Â
The Role of Asphalt Rejuvenators in RAP RoadwaysÂ
Asphalt rejuvenators were developed to address the challenge of using high-RAP mixes that meet performance requirements. An asphalt rejuvenator, or asphalt recycling agent, is designed to restore the functional properties of the aged bitumen in RAP mixes, resulting in similar performance when compared to non-RAP mixes. Â
Â
An ideal rejuvenator, like Sripath’s ReLIXER®, will soften bitumen, adjust binder grade, rapidly penetrate particles, aid compaction, restore functional balance in the mix, and aid durability. The results can be high-performing, long-lasting roadway surfaces comprised of high RAP. Â
Â
The ability to use high amounts of RAP directly reduces the need for virgin bitumen and fresh aggregate in a mix. However, not all rejuvenators have the same environmental impact. DOTs, contractors, and other agencies looking to incorporate a recycling agent into their mix design should also consider the sustainability of the rejuvenators themselves. Â
Â
Some rejuvenators are sourced from petrochemicals. These not only have a negative impact on carbon emissions during their production but can also expose workers to hazardous chemicals. In contrast, ReLIXER is based on a blend of bio-oils that are sustainability sourced from non-food crops. Independent environmental impact assessments have determined ReLIXER’s impact on Global Warming Potential (GWP) to be -1.451 per kg of CO2 eq. per kg of ReLIXER. Choosing the right rejuvenator should come down to a combination of performance data as well as carbon footprint of the actual product. Â
Â
Other Approaches to Sustainability in Asphalt PavementsÂ
The asphalt paving industry is widely focused on innovative approaches and technologies that will enable higher RAP usage to lower carbon emissions. However, using RAP is not the only way to further sustainable paving efforts. Â
Â
Smoother Roadway Surfaces Â
Creating roadway surfaces with fewer imperfections can have benefits beyond reducing wear and tear on vehicles. Improving roadways can mean enhanced fuel efficiency for vehicles, which can have significant environmental impacts. Research has shown smoother roadway surfaces, which typically reduce friction and obstacles that make vehicles work harder to cover distances, a lower fuel consumption by 4.5%. This equates to savings of 7 billion gallons, similar to removing 10 million vehicles from roadways annually. Â
Â
Warm Mix Asphalt TechnologyÂ
Typical asphalt mixes for roadway development use what is known as a hot mix asphalt (HMA) approach. HMAs are produced and mixed at temperatures ranging from 135-177°C (275-350°F) and compacted at temperatures between 104-143°C (220-290°F). Warm mix asphalt (WMA) is designed to be produced and compacted at significantly lower temperatures, between 30-120°F less than HMA. By using less energy to heat the mix throughout production, transportation, and compaction, WMAs help DOTs and contractors further reduce their own carbon emissions. The use of warm mix additives like PHALANX® enable these temperature reductions without compromising the integrity or performance of the roadway surface. Â
Â
Reducing Roadway Maintenance and RepairÂ
Considerations for sustainability in asphalt pavements should go beyond their initial construction. Roadway maintenance and repair have been significant contributors to carbon emissions. Reconstruction and restoration projects, from filling potholes to resurfacing failed roads, account for between 3,100 and 5,200 tons of CO2 emissions, not counting the emissions caused by congestion and delays that construction and maintenance projects can cause. By incorporating best practices for roadway design from the start, including the use of additives that can improve durability, reduce rutting, limit cracking, and improve fatigue resistance, additional carbon emissions can be saved across the roadway’s lifecycle.Â
 Â
Since its inception, Sripath has developed innovative additives designed to improve asphalt roadway performance while supporting sustainable paving practices. The Sripath product portfolio includes an array of additives that enhance bitumen properties, enable high-RAP use, and support performance outcomes for warm mix asphalt.Â
Â
To learn more about Sripath’s commitment to sustainability in asphalt, email info@sripath.com. Â
Â