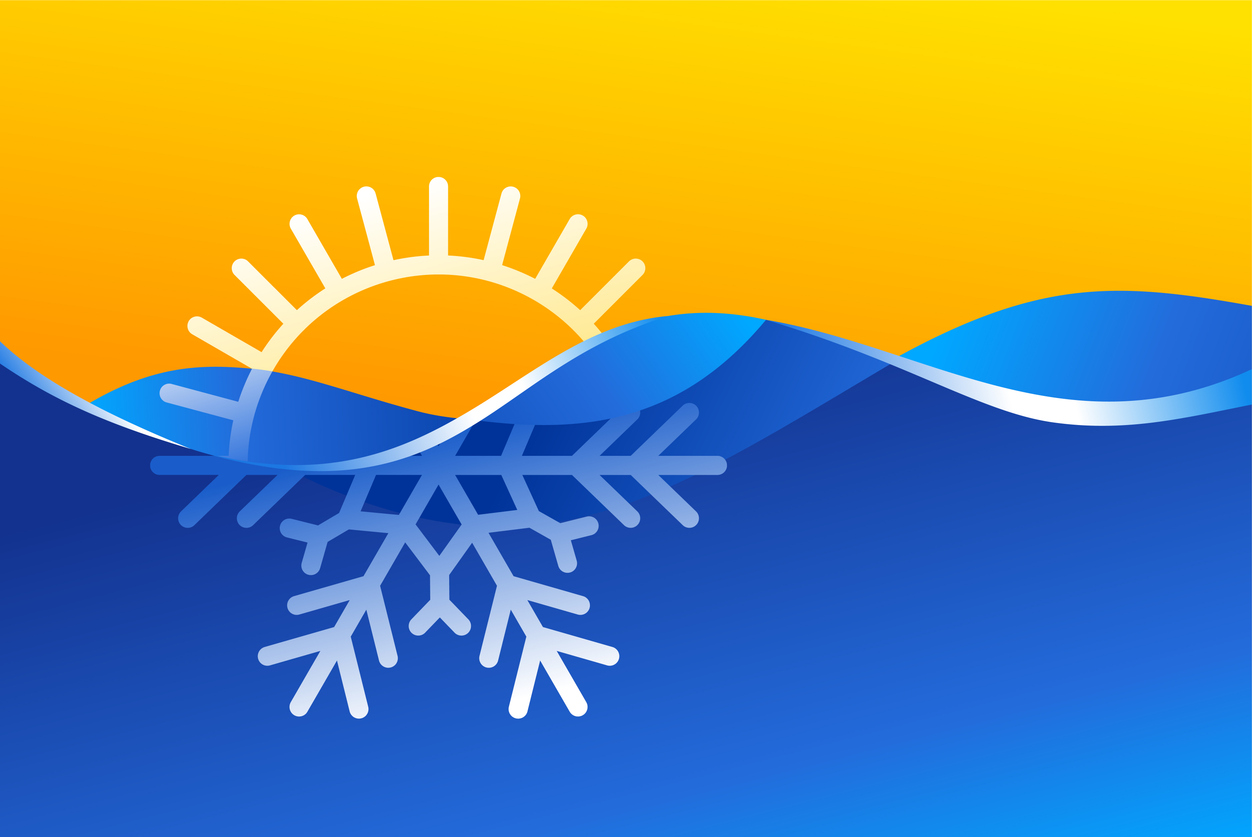
Warm mix additives for asphalt (WMAs) may be newer to the paving industry, but they are becoming increasingly important as contractors look to achieve density and smoothness of roadway surfaces while also meeting sustainability standards. These additives can help agencies achieve reduced emissions onsite and aid material compaction for potentially higher performing roads. Key to the process is the WMA’s ability to lower the temperature requirements for asphalt mixes during production, transportation, and application.  Â
Here, we will explore the evolution of warm mix additives and how this paving technology has helped contractors and departments of transportation meet their performance specifications and reduce their net carbon emissions. Â
Warm mix asphalt is paving mix that can be produced and compacted at lower temperatures than traditional hot mix asphalt materials for roadway development. Temperatures for warm mix asphalt can be between 30 to 120°F less than hot mix asphalt applications. Â
Â
Warm mix asphalt technologies are fairly new to the paving industry, with the first trials conducted in 1999. Since its introduction, warm mix asphalt applications are on the rise with nearly 40% of asphalt pavements in the U.S. manufactured using the technology including projects across 40 states. In Europe, warm mix asphalt roadways have been implemented for over a decade. Â
Warm mix additives are materials that can be incorporated into asphalt mixes to allow for lower production and compaction temperatures. These additives are designed to allow lower production and compaction temperature without changing binder characteristics such as Pen or PG Grade.Â
Warm mix additives have been proposed to work by lowering the viscosity of the binder in a mix. By doing so, the mix can be manufactured, transported, and compacted at lower temperatures. Warm mix additives can improve wettability by helping to lubricate and coat aggregates, making the overall mix material more workable. However, more recent thinking in the science of warm mix additives has focused on their role on improving wettability and lubricity of the coating around the aggregates, hence lowering the friction coefficient that allows for effective packing at lower temperatures.Â
Â
Organic additives are derived from waxes and fatty amides, requiring lower temperatures to improve lubrication. Chemical additives including emulsifiers and surfactants improve viscosity by reducing aggregate friction and energy. Water-based agents, or foaming agents, introduce water that converts to steam during heating to increase aggregate surface area and promote better coating of the aggregates with the binder. Â
Warm mix additives are typically classified into two groups – water and chemical additives (typically surface-active agents).Â
Warm mix asphalt typically includes formulated amounts of aggregate and binder, which can be made up of virgin materials, reclaimed asphalt pavement (RAP), or a combination of both. The binder used may be conventional (neat) binders or polymer modified bitumen (PMB) binders. The mix is then dosed with a warm mix additive to enable the material to be blended and compacted at lower temperatures than standard hot asphalt mixes. Â
Warm mix additives allow for asphalt to be produced and compacted at lower temperatures than traditional hot mixes. This may result in reduced greenhouse gas (GHG) and asphalt emissions through lower operational temperature requirements at the plant and at the job site. Using 20-75% less energy to produce than hot mixes, warm mix asphalt may also lower overall costs. Paving crews also report achieving density and smoothness on pavements more easily on warm mix asphalts under a wide variety of conditions.Â
Â
The lower temperature also makes for safer conditions for workers who are subjected to less heat and fumes. Warm mix asphalt can also be transported further from plants than traditional asphalt mixes, opening up operational opportunities for plants and contractors. Paving seasons are also extended when using warm mix technology since the material can be paved with lower ambient temperatures. Â
Warm mix asphalt requires significantly less energy to produce than traditional hot mixes because the temperature requirements for production and compaction are lower. Heating of raw materials accounts for 60% of fuel consumption at a plant. Warm mix technology can reduce fuel consumption through lower temperature requirements by up to 20%. Reducing energy and fuel consumption has a direct impact on carbon emissions and resource depletion. Warm mix application may produce less smoke, odors, and fumes that are harmful not only to workers but also to the environment. Warm mix asphalt roadways have also been found to perform equally well as hot mix asphalt surfaces. Â
Different additives will have different blending guidelines. However, warm mix additives are typically added blended with the binder at the plant. The combined mixture is then blended with aggregates to make the final asphalt mix. Â
Hot mix asphalt (HMA) is produced and mixed at temperatures ranging from 135-177°C (275-350°F) and compacted at temperatures between 104-143°C (220-290°F). By comparison, warm mix asphalt is manufactured and compacted at significantly lower temperatures between 30-120°F less than HMA. It is hypothesized that due to lower temperatures used, the binder ages less while using WMA than HMA. WMAs may also be less expensive to produce given the lower energy consumption requirements dictated by lower temperatures. Â
Most warm mix additives for asphalt are designed for compatibility with different grade bitumen or asphalt mixes. This includes neat and polymer modified bitumen (PMB). Â
Warm mix asphalt can typically be produced at temperatures between 115-135°C (240-275°F) and compacted at temperatures above 107°C (225°F).Â
Warm mix additives are typically compatible with other additives or polymer modified bitumen (PMB) mixes. Compatibility testing is essential to ensure safe use and performance outcomes. Typically, WMAs do not impact binder characteristics.Â
One of the many benefits of using warm mix asphalt is its ability to aid in compaction. Lower required compaction temperatures achieved through the use of effective warm mix additives may also result in helping contractors meet their void volume in asphalt, or voids in mineral aggregate (VMA), specifications. Â
Warm mix asphalt can be used across pavement thicknesses and varies depending on use and expected traffic volume. Warm mix asphalt can be used for applications including the wearing course as well as the binder course. This layering technique can help roadways reach longer lifespans despite heavy traffic and severe weather conditions. Â
Warm mix additives require lower temperatures during application, making the work site safer for workers. The lower temperatures also produce less harmful odors and fumes. Warm mix asphalt paving has the potential to create lower concentration of breathable particulate matter and organic carbon compared to hot asphalt paving. Â
Introducing a warm mix additive does not notably adjust performance grade (PG) of mixes or other binder characteristics. Appropriately dosed balanced mixes should not be affected in terms of durability, cracking, rutting, or fatigue. Â
Most warm mix additives can be incorporated into mixes containing other additives such as polymers, anti-strip agents, fillers, and fibers. Combining WMAs with polymer modified bitumen (PMB) is becoming a more common practice as contractors consider both pavement construction and sustainability in asphalt. Â
Â
WMA use such as PHALANX® to lower production and compaction temperatures of the mix with a polymeric additive like PGXpand® to improve rutting and fatigue can create a mix designed for workability and long-term performance. Â
Â
WMAs can also be combined with an effective rejuvenator like ReLIXER® to increase the amount of reclaimed asphalt pavement (RAP) incorporated into a mix. The rejuvenator or recycling agent can restore the functional properties of the aged binder without negatively impacting performance. This can provide a more sustainable approach to paving without sacrificing durability. Â
Since warm mix additives lower compaction temperatures, roadways using warm mix asphalt can be built during colder weather conditions than traditional hot mix asphalt roads. This can help contractors extend their paving seasons into cooler months. However, rainy seasons may impact construction windows depending on localized climate since dry conditions are ideal for installing new roadway surfaces.Â
Warm mix asphalt requires lower compaction temperatures. This can increase haul distances between plants and job sites since there are fewer concerns about the material arriving cold at the jobsite.Â
Effective warm mix additives for asphalt are designed to help lower production and compaction temperatures of the mix. WMAs can be used to dose a mix that includes reclaimed asphalt pavement but should have no bearing on performance. Incorporation of high amounts of RAP in the mix can require the addition of an effective rejuvenator to restore the functional properties of the aged bitumen in the RAP.Â
Recommended dosing for warm mix additives in asphalt mixes will vary depending on a variety of factors including the dosage efficiency of the selected WMA, weather conditions, and asphalt mix composition. Â
Warm Mix Additives for Asphalt and PHALANX®Â
PHALANX, a superior warm mix additive, is designed to improve compactability of hot asphalt mixes and polymer modified bitumen (PMB) mixes. It helps both production temperatures and compaction temperatures required when laying down a roadway. PHALANX may also help lower carbon emission, reduce energy consumption, and deliver overall cost savings.Â