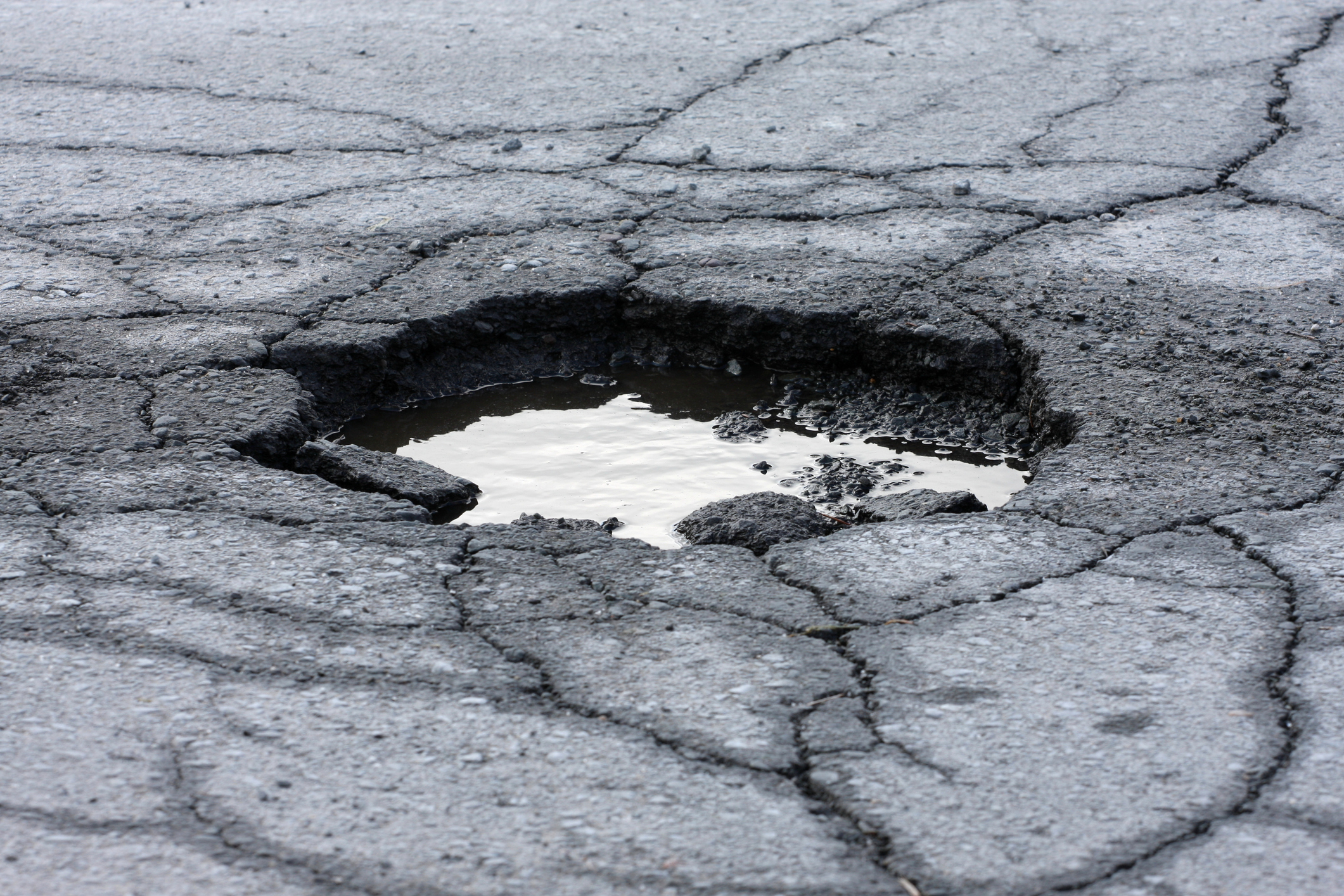
New roadway infrastructure development is on the rise with market growth of 8.05% expected by 2032. This demand is due, in part, to the deteriorating condition of existing roadways. In fact, in the U.S. alone, 39% of roads are considered to be in poor or mediocre condition. Â
Â
The primary culprit behind substandard roadway conditions: potholes.Â
Â
Damage to passenger vehicles mounts to a U.S. national average of $406 per car, while (depending on contract terms) roadway crews may be called back to make repairs costing nearly $200 per imperfection. Nearly 630,000 potholes were reported across England, Scotland, and Wales in 2023 with data from only 55% of councils available. In New Jersey alone, approximately 135,000 potholes were repaired or filled in 2023, costing taxpayers $1.8 million. Â
Â
Potholes are costly beyond the hard currency. They also inhibit mounting sustainability goals. Uneven road surfaces cause vehicles to consume more fuel, and so maintaining smoother surfaces free of potholes can improve greenhouse gas emissions (GHG) by up to 2%. Crews called out to roadway locations to conduct the repairs also contribute to carbon emissions with everything from material transportation to the production of the asphalt mix used to fill the pothole.Â
Â
With potholes, prevention is often the best course of action rather than an expensive, environmentally unfriendly repair and replacement approach. Typically, potholes are a function of several causes including: Â
Â
- Age and condition of the pavement Â
- Environmental conditions Â
- Traffic type and frequency Â
- Moisture sensitivity Â
- Construction defects Â
Â
The selection of appropriate materials and a well-designed mix are very important. Proper mix production at the plant, as well as laydown and compaction, are essential for long-term performance. Achieving the required smoothness is also very important. When it comes to construction best practices, here are four key methods for preventing roadway potholes during asphalt application to optimize onsite operations and avoid costly callbacks.Â
Â
- Keep the paving equipment clean: Crews should take the extra few minutes to ensure that the tools that will come in contact with an asphalt mix are properly prepared. That means using a release agent for everything from plate compactors to hand tools. The release agent will help keep the asphalt from adhering to equipment surfaces as the roadway is installed and leaving small defects behind that can grow into much bigger divots, and potholes, over time. Â
- Avoid Surface Defects: Optimal roadways are graded and leveled to support drainage and produce smooth surfaces. Crew members who must cross or stand on a newly constructed roadway surface should use specially designed tamp shoes that will not leave tracks or indents behind. These depressions can unnecessarily lead to cracking and potholes. Â
- Minimize Transverse Joints: Another way to avoid potholes is to limit bumps or disruptions in the roadway surface that can lead to cracking or breakage. This can occur when using transverse joints which, while allowing for temperature contraction, can introduce vulnerabilities to the asphalt. Instead, contractors should plan to continuously move the paver, optimally operating during suitable weather conditions and rotating crews to avoid stoppages. Â
- Control Mix Temperature: Even when dealing with warm mix asphalt, temperatures can heat up on the job site. However, maintaining ideal compaction temperatures requires more than monitoring the hopper. Contractors should ensure the screed is heated properly as it handles the asphalt on its way to the roadway surface. If the mix, or the tools used to install it, are too cool, roadway density can be affected and lead to rougher surfaces that can trap water, lead to cracking, and introduce potholes. Mitigating segregation is always paramount.Â
Â
While these techniques can help reduce the introduction of potholes into new roadways, dealing with existing damaged surfaces is a present reality. Fortunately, repair and maintenance applications have advanced to help reduce environmental impact through the use of high-RAP mixes (up to 100% in some instances) for pothole patching. Since RAP is comprised of aged bitumen, an effective asphalt rejuvenator or recycling agent should be added to the mix to restore the bitumen’s functional properties. Â
Â
To achieve this, hot patch and cold patch mixes can be dosed with an asphalt rejuvenator like ReLIXER®. Highly efficient with low dosing levels, easy to incorporate via mobile drum mixers, and non-hazardous to handle, ReLIXER also helps lower GHG as an environmentally friendly bio-based oil additive.Â
Â
Learn more about ReLIXER for repair and maintenance projects. Â
Â