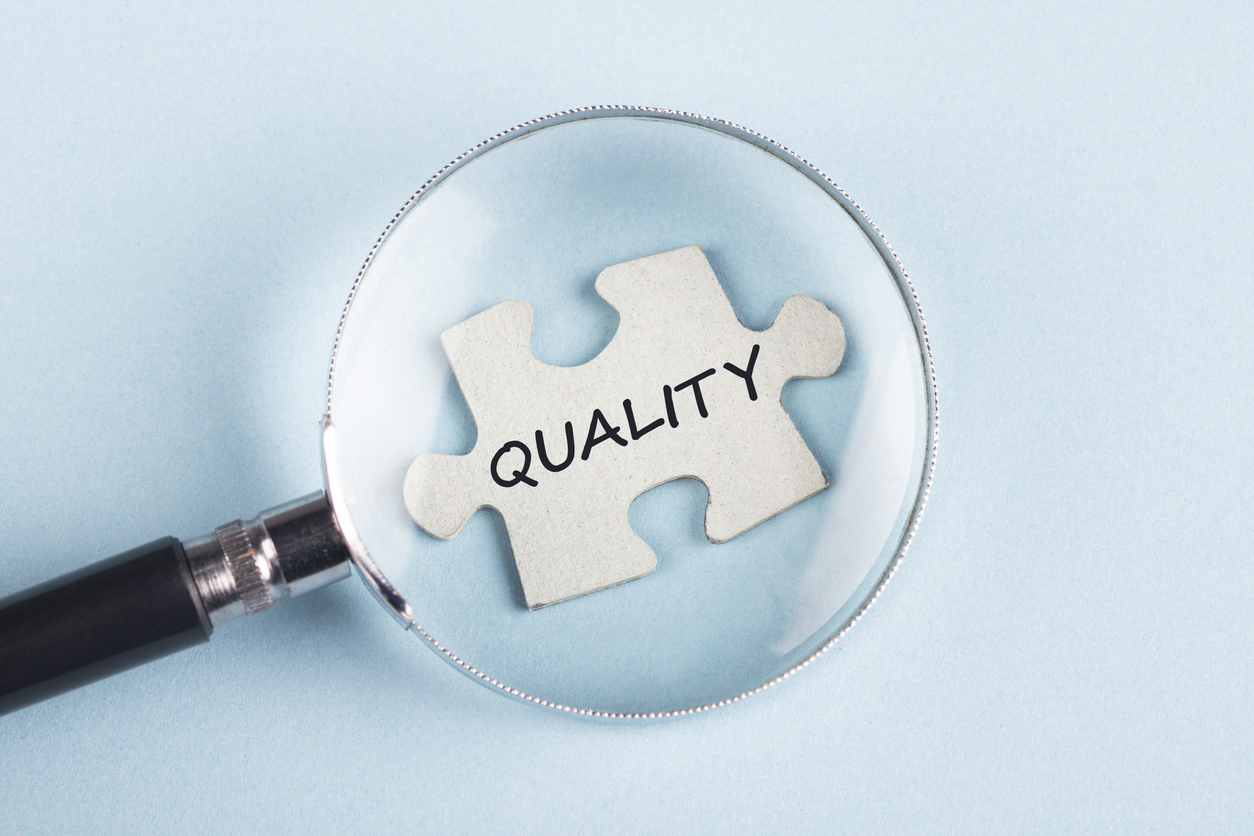
Modern crude oil refining and bitumen production technologies are having a global impact on bitumen quality, consistency, and functionality. As a result, the industry is shifting to a new mentality of developing clear, attainable performance criteria to design quality mixes without relying on suppliers to dictate quality. Â
Here, we will take a closer look at bitumen quality and the shifts taking place in today’s bitumen marketplace including changes to how bitumen is sourced, procured, and incorporated into balanced mix design to address performance. Â
Bitumen Quality and Sripath®Â
Sripath understands that bitumen quality is more inconsistent than ever before as plants and contractors grapple with stringent performance requirements and globally sourced, variable bitumen for their mixes. Sripath’s diverse product portfolio includes solutions that enhance bitumen performance by adjusting the functional properties of mix. The result can be paving and roofing solutions that exhibit durable performance while adhering to sustainability guidelines. Sripath’s innovative engineered materials include a range of rejuvenators, oils, and polymers that enhance performance while remaining cost effective. Â