Recycle & Reuse High Levels of RAP
Impact of Using Higher Levels of RAP
Roadway deteriorate over time, resulting in raveling, cracking, and fatigue damage. Globally, over 750 million tons of RAP are generated annually. On an average, only less than 20 %, of RAP is recycled, the rest ships to landfills.
To accommodate growing needs, there is an need to expand the global network of roadways. This results in the increased depletion of natural resources, such as virgin bitumen and aggregates.
The industry is attempting to maximize RAP usage. It has been demonstrated that there is a reduction in Green House Gases (GHG) with increasing RAP usage. Increasing RAP from 0% to 60%, the total GHG emissions decreases from 72 to 51 Kg of CO2 [Courtesy: N Michel, AfPA Tech Talk, Nov 23, 2021].
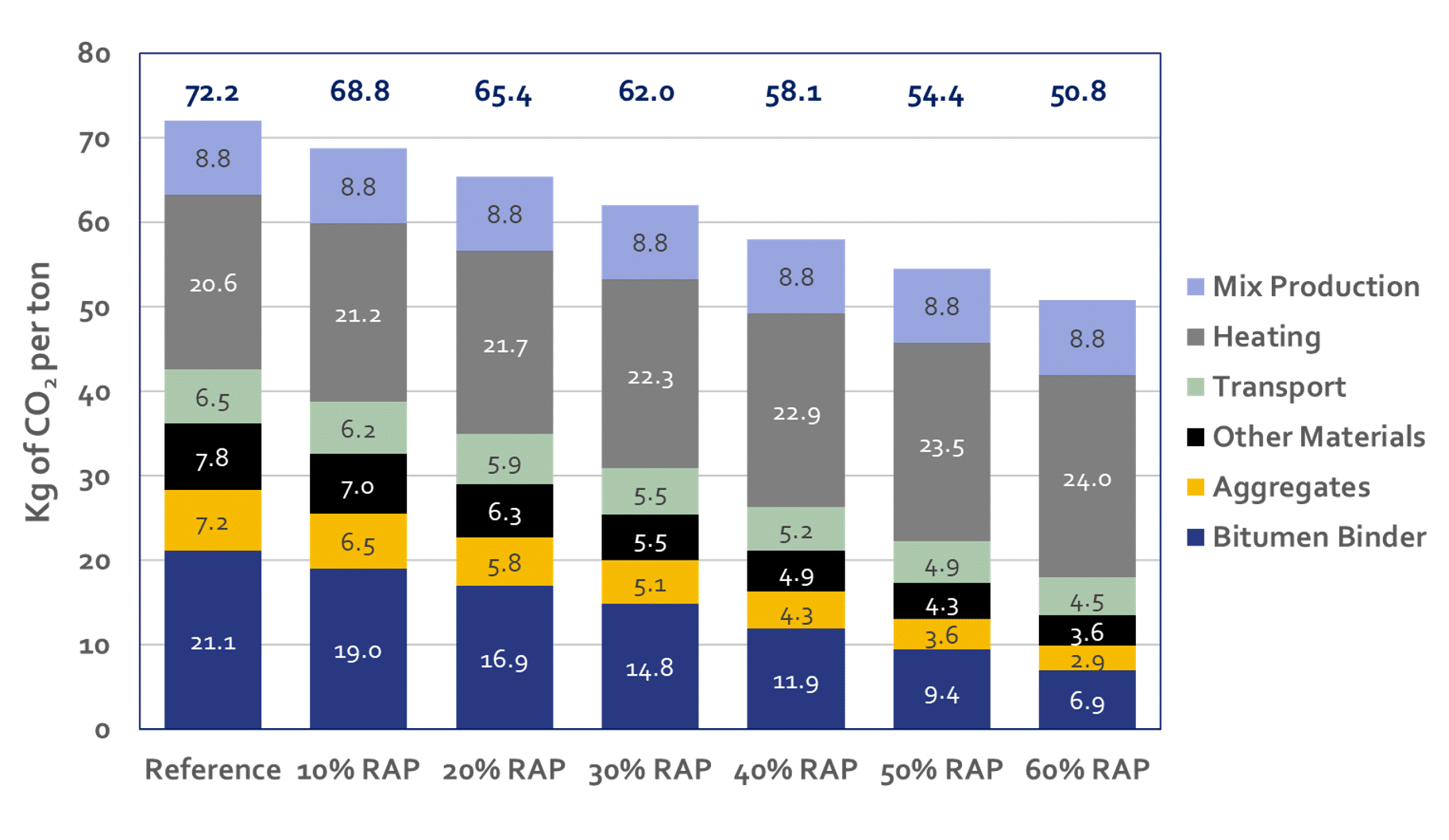
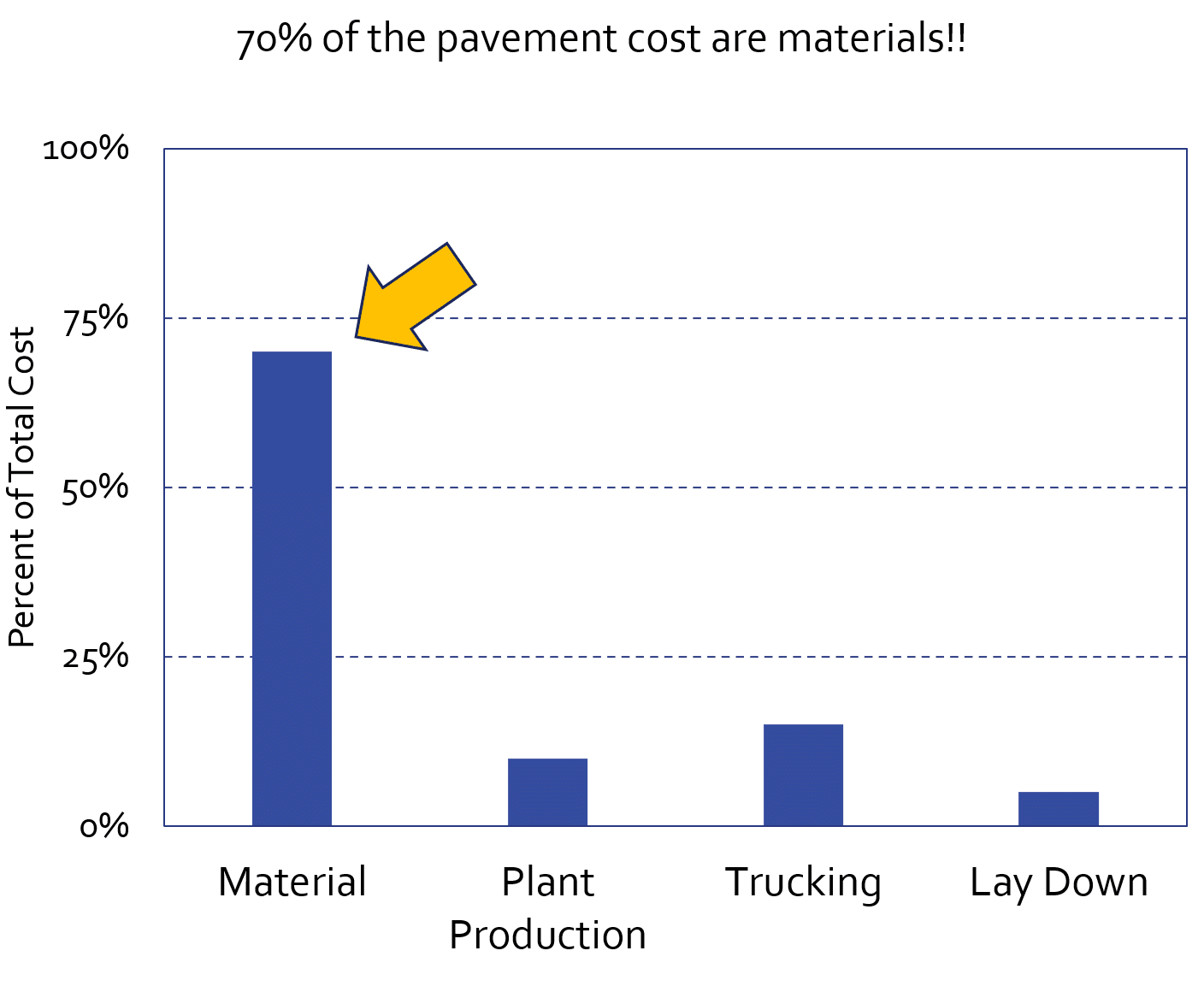
The Economic Case for Greater RAP Usage
[Courtesy: FHWA-HRT-11-021]
Environmental Impact vs. Economic Viability vs. Roadway Performance

Balanced Mix Design Approach to Optimize High-RAP Mixes
For Greater than 25 % to 30 % RAP a REJUVENATOR is Needed
- Seek a balance between Rutting and
Fracture Toughness properties - Rutting: Hamburg, APA, Cooper, French Wheel, Cantabro, etc.
- Fracture Toughness: Overlay, SCB, SENB,
I-FIT, DCT, Ideal CT, etc. - Costs
- Potential Cracking
- Potential Rutting
- Potential Fatigue
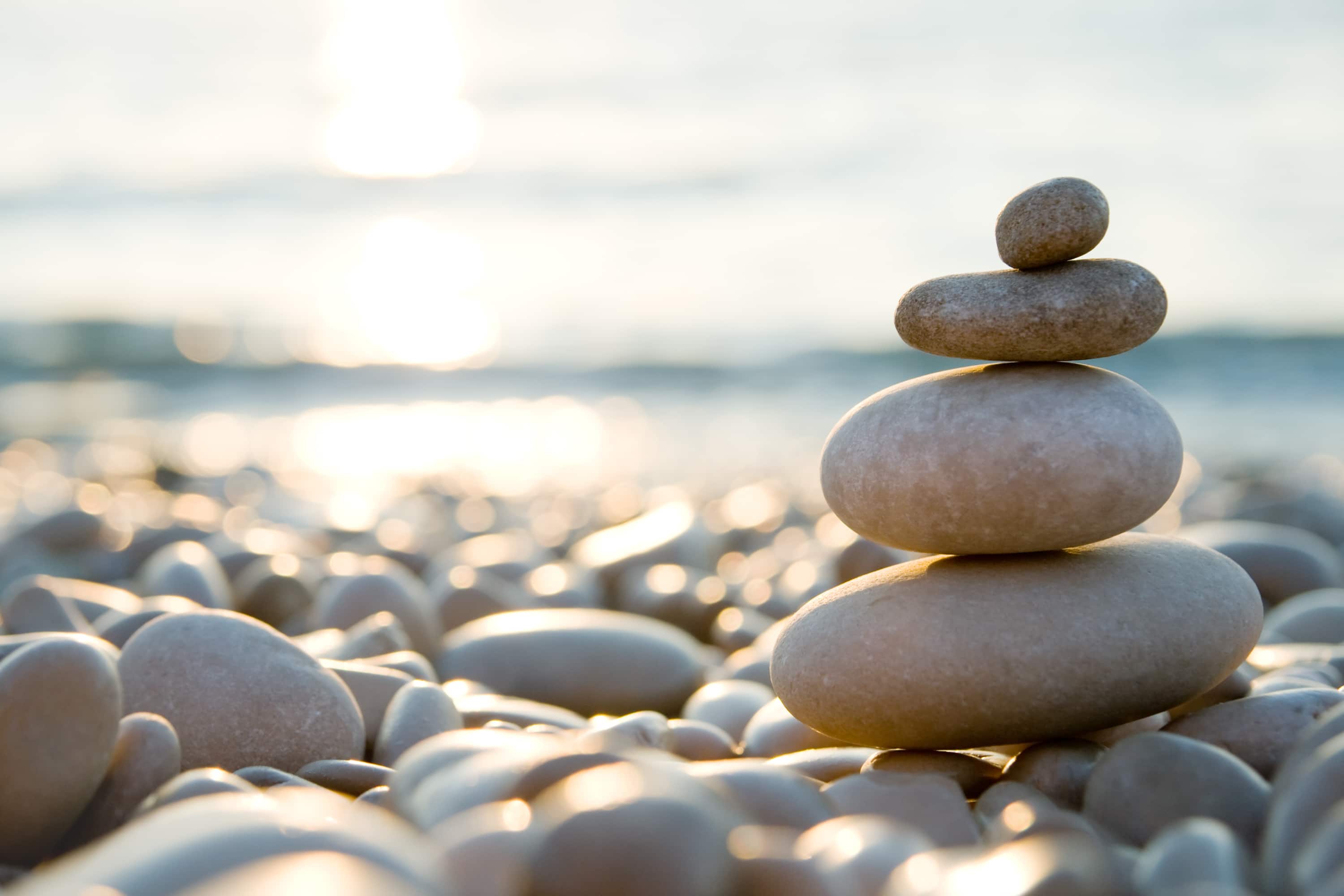
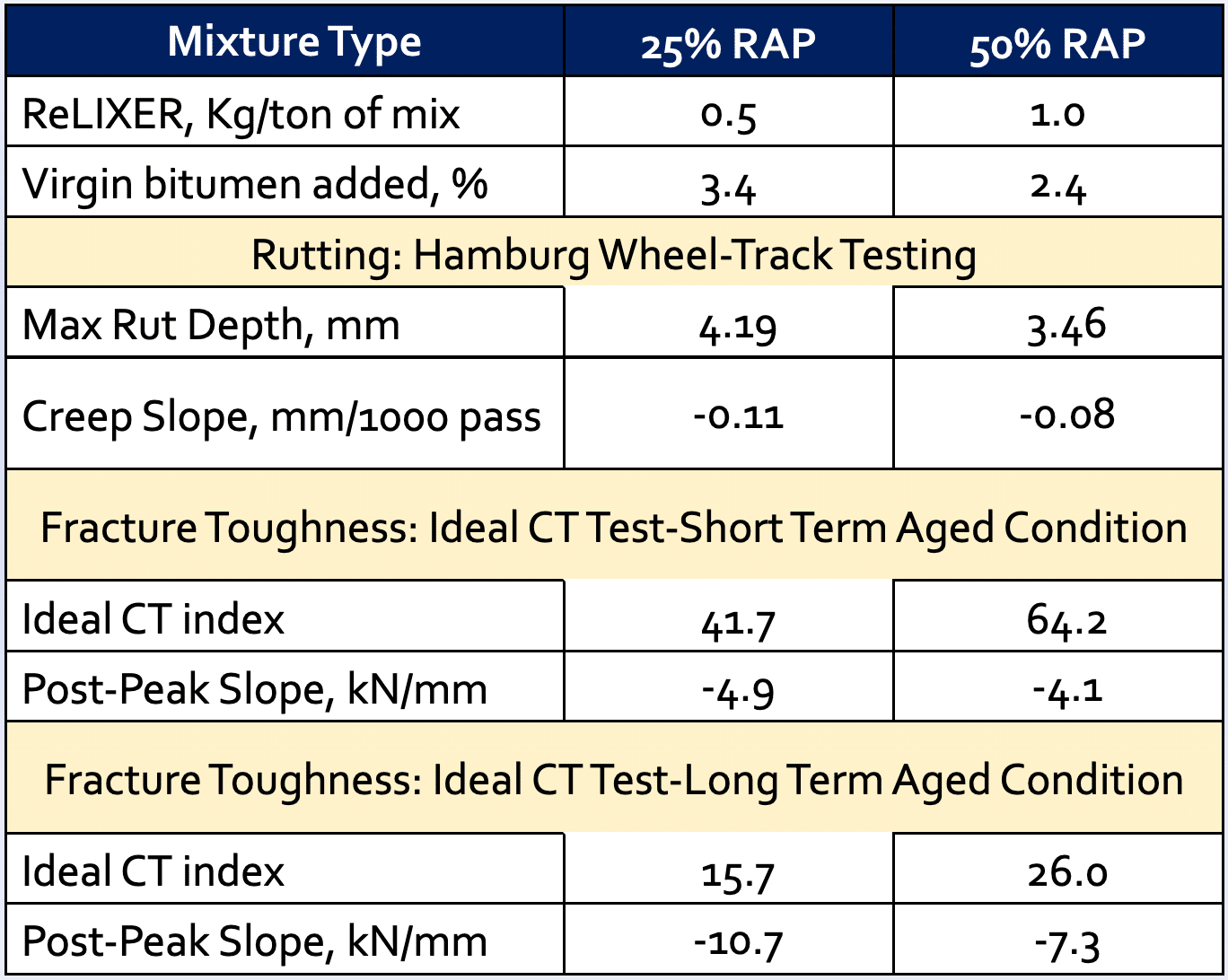
ReLIXER®: Impact on Resistance to Rutting & Cracking
The concept of balanced mix design was employed to design an idea for a wear layer application in the USA.
Two high-RAP Mixes, 25 % RAP and 50 % RAP were evaluated. The 25 % RAP Mix contained 0.5 Kg per ton of ReLIXER and 3.4 % virgin bitumen, PG 64-22. The 50 % RAP Mix contained 1 Kg per ton of ReLIXER and 2.4 % virgin bitumen. The total amount of liquids was targeted around 5.6 %.
Both the Mixes resulted in an excellent balance between rutting resistance and fracture toughness properties
Deeper Insight